There is no doubt that energy storage is proliferating right now. Demand has grown significantly in recent years which has resulted in a significant price drop of lithium-ion batteries. This price drop has enabled many more large-scale lithium-ion installations and, with this, has prompted regulatory and certification agencies to begin enacting standards for these systems.
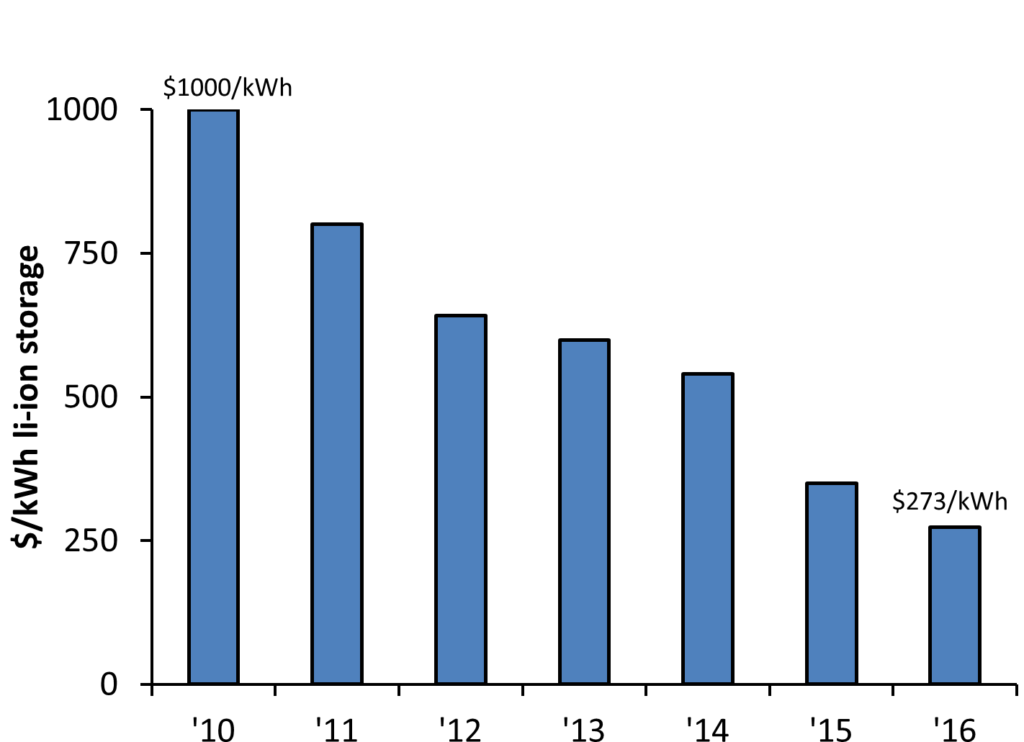
A common way for these agencies to evaluate a system is to mandate a lithium-ion battery DFMEA, which is a design failure modes and effects analysis.
DFMEA: Design Failure Modes and Effects Analysis
A DFMEA evaluates and quantifies risk for a given system. By compiling a bill of materials (BOM) of your system with product definitions, you assign three variables to each given component in the BOM. These variables are quantified by the following questions:
- What is the severity of a failure that would result from a component malfunction? (1-10 scale, 1 no effect, 10 hazardous)
- How likely is this malfunction to occur? (1-10 scale, 1 failure is normal, 10 failure is unlikely)
- How likely is your system to detect the malfunction? (1-10 scale, 1 certainty of detection, 10 uncertainty of detection)
These values are then multiplied to give the RPN of each component. The resulting value helps identify component failure modes and their resulting effects.
RPN = (Severity) * (Occurrence) * (Detection)
A DFMEA is a compilation of RPN values for every component of a system. This compilation of information creates a valuable tool for understanding system vulnerabilities and better improving the safety through reliable fault detection technologies.
Large-scale lithium-ion battery systems have hundreds of components and each component has its own failure mode. A lithium-ion battery DFMEA should be addressed as early as possible and continuously updated and improved throughout the project.
Once vulnerabilities in the system are understood, acknowledging the need for and implementing detection technologies for failures is critical. Of the sensor types that exist, some will be more appropriate than others for lithium-ion battery systems. Temperature, voltage, current, and off-gas monitoring are great examples of sensing technologies that are integrated into lithium-ion battery systems.
The Li-ion Tamer AWARE is a great example of a fault detection technology for lithium-ion batteries. The AWARE monitors for off-gas compounds which are often detectable several before thermal runaway by several minutes, giving an early warning of impending failure.
By incorporating an off-gas monitoring product into a lithium-ion battery system, you help detect a fundamental failure mode in a lithium-ion battery, an off-gas event. Having awareness of these events provides an extra layer of protection against catastrophic failures. Utilizing off-gas monitoring, as well as other monitoring technologies, will help decrease your “N” value in the RPN of a DFMEA, making your system less likely to fail and decreasing vulnerabilities of a battery as a whole.
Let’s Get Started |
|
---|---|
Take the first step in improving the safety of your battery storage systems by requesting the Rack Level Monitor today! Simply click on the button below to complete and submit the form. |